Inhaltsverzeichnis
Abstract
Ziel dieses Aufsatzes ist die Erörterung der Einsatzmöglichkeit von IO-Link im Hinblick auf Effizienz und Kosteneinsatz von Maschinen. Hierfür wird zunächst auf die komplexer werdende Kontrolle von Maschinen eingegangen, dann werden die verschiedenen Kommunikations- bzw. Steuerungssysteme für Maschinenkomponenten sowie die Eigenschaften von IO-Link und „IO-Link wireless“ inklusive der jeweils entstehenden Vorteile erörtert. Abschließend wird beschrieben, wie IO-Link mehr Effizienz bei der Produktion und Kostenersparnisse beim Maschinenbau ermöglicht.
Motivation / Auslöser
Aufgrund des marktwirtschaftlichen Wettbewerbs zwischen Unternehmen ist es notwendig, ein Produkt mit der bestmöglichen Kosteneffizienz herzustellen.
Dies betrifft vor allem den maschinellen Produktionsprozess, da u.a. Automatisierung, Geschwindigkeit, Wartbarkeit und Zuverlässigkeit bedeutende Faktoren bei der Herstellung sind.
Beim Steuern der Maschinen selbst müssen u.a. die Daten von den Sensoren und die Befehle an die Aktoren organisiert werden, was eine effiziente Steuerungstechnik erfordert.
Es sind derzeit verschiedene Standards für die Kommunikation mit den verschiedenen Komponenten auf dem Markt, die jeweils ihre Stärken bzw. Vorteile haben, jedoch durch ihre Schwächen bzw. Nachteile z.B. Ineffizienz/ineffiziente Produktionsschritte verursachen oder die Zuverlässigkeit nicht garantieren können.
Der IO-Link-Standard hat jedoch alle Stärken, die für den kostengünstigen Bau von effizienten Maschinen notwendig sind, ohne dass seine Nachteile zu nennenswerten Problemen führen.
Stand der Technik
Es gibt gegenwärtig verschiedene Kommunikationsstandards, die die anfänglich genutzte, aber teure, Parallelverdrahtung weitgehend abgelöst haben (vgl. [1]). Die bekanntesten Standards für die Maschinensteuerung sind die Feldbussysteme, industrielles Ethernet und IO-Link, deren Vor- und Nachteile einander gegenübergestellt wie folgt aussehen:
Die verschiedenen Feldbus-Systeme bzw. -Varianten erlauben eine leichtere Installation, mehr Zuverlässigkeit und mehr Flexibilität im Vergleich zur parallelen Verdrahtung. Jedoch benötigen sie als ein komplexeres Konzept qualifizierte Mitarbeiter, teurere Komponenten und mehr Zeit für die Kommunikation. Des Weiteren verursacht die Existenz von verschiedenen Systemen bzw. Umsetzungen mehr Aufwand bei der Auswahl, Installation und Konfiguration der Komponenten (vgl. [1 und 2]).
Industrielles Ethernet ist im Vergleich zu den Feldbussystemen hingegen in der Lage, größere Datenmengen, Echtzeitdaten und IT-Daten gleichzeitig zu übertragen sowie große Netzwerkausdehnungen und sehr hohe Teilnehmerzahlen zu erreichen, während die Teilnehmer selbst gleichberechtigten Zugriff auf die Busse haben. Dabei können verschiedene Übertragungsmedien kombiniert werden. Allerdings verwendet es aufgrund seiner Wurzeln im Ethernet einen Kabelstandard, der u.a. für die Telefonie verwendet wird und theoretisch nur in Büroumgebungen zuverlässig ist. Die Signalqualität der Ethernetkabel ist daher anfällig für fabrikbedingte Störfaktoren wie „Vibrationen, Schmutz, Feuchtigkeit, schädliche Substanzen und EMV-Strahlung“ [3]. Diese Schwäche macht es trotz seiner Vielseitigkeit und Mächtigkeit weniger geeignet für den Einsatz innerhalb von Maschinen, in denen zumindest einer dieser Faktoren in hoher Intensität vorkommt. Jedoch kann es durch die Forschung zu Fortschritten und Verbesserungen kommen (vgl. [3]).
Auf den IO-Link-Standard wird im folgenden Kapitel eingegangen und seine Eigenschaften im Vergleich zu den beiden vorherigen Möglichkeiten erörtert (vgl. [4]).
Analyse, Diskussion und Bewertung
Ein IO-Link-System besteht aus IO-Link-Mastern, IO-Link-Devices (Input und Aktoren), Leitungen und einem Konfigurationsprogramm für IO-Link. Die Master dienen als Kontroller für angeschlossene Devices oder untergeordnete Master (vgl. [4]).
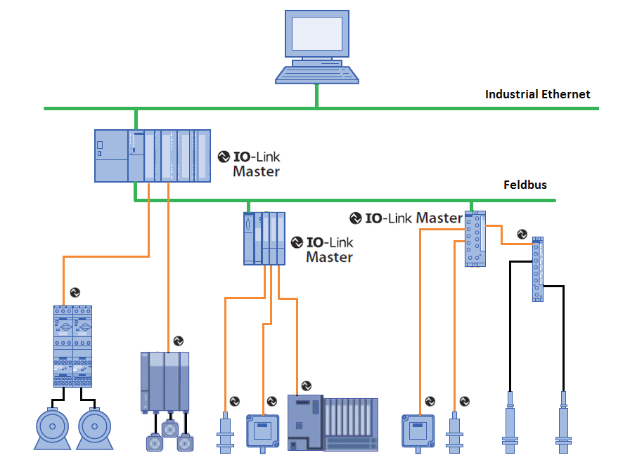
Die IO-Link-Schnittstelle ist eine „serielle, bidirektionale Punkt-zu-Punkt-Verbindung“ [4], die Signale übertragen und angeschlossene Komponenten mit Energie versorgen kann.
Es werden üblicherweise für Sensoren 4-polige Stecker und für Aktoren 5-polige Stecker verwendet. Die Pin-Belegung ist wie folgt standardisiert: Pin 1 liefert als Plus-Pol 24 V Spannung, Pin 3 als Minus-Pol 0 V und Pin 4 dient dem Schalten und Kommunizieren (C/Q). Der dabei mögliche Strom beträgt höchstens 200 mA.
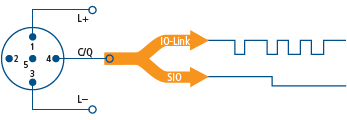
Für die IO-Link-Master hingegen gibt es zwei Porttypen: Typ A bzw. Port Class A, der keine Vorgaben hinsichtlich der Funktionen der Pins 2 und 5 macht, sondern den Hersteller diese festlegen lässt, und Typ B bzw. Port Class B, der eine 5-Leiter-Standardleitung nutzt und über die Pins 2 (2L+) und 5 (2M) galvanisch getrennte Versorgungsspannung bereitstellt.
Für das Verbinden von den Devices mit dem Master wird jeweils eine ungeschirmte 3- bzw. 5-adrige Standardleitung von maximal 20 Metern Länge verwendet (vgl. [4]).
Diese Eigenschaften bringen die Vorteile, dass die Kabel preisgünstig, geprüft verfügbar und zuverlässig sind und das Anschließen von Komponenten leicht und schnell erfolgt (vgl. [5]).
Das Kommunikations-Protokoll von IO-Link ist wie folgt definiert:
Die Ports von Mastern können entweder für die typische IO-Link-Kommunikation festgelegt werden oder auch als Digitaleingang, Digitalausgang oder deaktiviert eingestellt werden.
Es gibt hierbei drei Übertragungsraten: COM 1 mit 4,8 kBaud, COM 2 mit 38,4 kBaud und COM 3 mit 230,4 kBaud. Der IO-Link-Master kann sich nach Spezifikation V1.1 an die mögliche Übertragungsrate der Device anpassen. Die Reaktionszeiten von Devices setzen sich jeweils aus dem minimalen oder fest eingestellten Zeitabstand zwischen den Aufrufen von dem Master an das Device und der internen Bearbeitungszeit des jeweiligen Masters zusammen (vgl. [4]).
Das Kommunikationssystem ist auch sehr robust, weil es mit einem 24 V-Pegel arbeitet und vor einer Fehlermeldung pro Übertragung bis zu drei Übertragungsversuche unternimmt. Es gibt vier Datenarten, wobei die Prozessdaten und deren Gültigkeit zyklisch und die Gerätedaten und Ereignisse azyklisch sind. Je Device werden Prozessdaten bis zu 32 Byte groß. Gerätedaten „[…] können Parameter, Identifikationsdaten und Diagnosedaten sein“ [4] und werden von Mastern angefordert oder übermittelt (vgl. [4]).
Man hat also die Vorteile, dass man bis in die kleinsten und einfachsten Sensoren den vollen Funktions-, Diagnose- und Einstellungs-Umfang hat und die Sensor-Einstellungen in den Mastern gespeichert werden (vgl. [6]). Des Weiteren kann man hierdurch auch alte Devices weiterhin nutzen und so Kosten sparen (vgl. [8]).
Der Zugriff auf die Devices wird auch durch das Definieren von Geräteprofilen vereinfacht. Diese definieren alles hinsichtlich der Kommunikation und Nutzung von den betreffenden Devices. Man kann also eine Vielzahl von Sensoren gleicher Bauart einheitlich verwalten und die jeweiligen Zugriffe der Steuerung auf sie erfolgen identisch (vgl. [4]).
Für alle Devices steht die jeweilige IODD (IO Device Description) bzw. jeweils die Beschreibung mit sämtlichen technischen Eigenschaften bereit, damit alle Komponenten herstellerunabhängig gleich benutzt werden können. Die Konfigurationsprogramme der verschiedenen Masterhersteller können diese einlesen, alle Devices und Ports konfigurieren und von allen angeschlossenen Devices Diagnosen durchführen (vgl. [4]).
Dies bringt folgende Vorteile: Alle Einstellungen werden gespeichert und nach einem Geräteaustauch automatisch übertragen und durch Identifikation werden Verwechslungen vermieden. Durch die integrierte Diagnosemöglichkeit mit den normalen Leitungen werden der jeweilige Zustand und möglicher Verschleiß erkannt und die Wartung erfolgt nur noch nach Bedarf (vgl. [7]).
Außerdem ist IO-Link kompatibel zu der Benutzung von verschiedenen IO-Link-Versionen: Master nach V1.1 können die Devices nach V1.0 und V1.1 betreiben, wobei von Devices nach V1.0 die Datenübertragungsrate 230,4 kBaud und die Parametrieserverfunktion (Datenspeicher) nicht unterstützt werden. Master nach V1.0 können alle Devices nach V1.0 betreiben (vgl. [4]).
In der heuten Zeit werden die Komponenten von Maschinen auch kabellos über Funk miteinander verbunden und manche Maschinen würden an physischen Verbindungen zu wartungsintensiv werden. Deshalb wurde IO-Link wireless entwickelt. Es wurde darauf konzipiert, dass alles genau so funktioniert wie mit dem normalen IO-Link, abgesehen davon, dass man für das Verbinden Funkadapter verwendet. Die Zuverlässigkeit der Verbindung wird hierbei gewährleistet, indem im Gegensatz zu Bluetooth die Lücken zwischen den WLAN-Kanälen genutzt werden. Die Verwendung von WLAN und Bluetooth im selben Bereich würde in den überlappenden Frequenzen zu Kommunikationsstörungen führen (vgl. [9]).
Insofern hat man bei der Nutzung von IO-Link wireless die Vorteile vom normalen IO-Link, die der zuverlässigen Verbindung und dass man ein einheitliches System nutzt.
Fazit
IO-Link und seine wireless-Variante zusammen haben keine nennenswerten Nachteile gegenüber den anderen Standards, sondern trotz der Einfachheit seitens der Anschlüsse und Kabel eine erstaunliche Anzahl an nützlichen Eigenschaften und Vorteilen (siehe oben). Insofern lassen sich durch das kostengünstige IO-Link und IO-Link wireless die Komponenten von Maschinen effizienter vernetzen und verwalten als es durch Feldbus und Ethernet möglich wäre.
Durch die gute Vernetzung und Kommunikation zwischen den Sensoren und den Aktoren durch IO-Link lassen sich sicherlich auch passende Maschinen für die voranschreitende Industrie 4.0 konstruieren.
Literatur
- [1] https://www.kunbus.de/feldbus-grundlagen.html (3.3.2018)
- [2] http://www.feldbusse.de/Vergleich/uebersicht_feldbusse.shtml (2.3.2018)
- [3] https://www.kunbus.de/industrial-ethernet.html (3.3.2018)
- [4] http://io-link.com/share/Downloads/At-a-glance/IO-Link_Systembeschreibung_dt_2016.pdf (2.3.2018)
- [5] http://io-link.com/de/Technologie/Montage_Inbetriebnahme.php?thisID=101 (5.3.2018)
- [6] http://io-link.com/de/Vorteile_mit_IO-Link/Entwicklung.php?thisID=100 (5.3.2018)
- [7] http://io-link.com/de/Vorteile_mit_IO-Link/Wartung.php?thisID=104 (5.3.2018)
- [8] http://io-link.com/de/Technologie/WusstenSieSchon/WusstenSieSchon_Abwaertskompatibel.php (6.3.2018)
- [9] Vortrag „Sensorvernetzung mit IO-Link und IO-Link wireless“, https://ilias3.uni-stuttgart.de/goto_Uni_Stuttgart_file_1370028_download.html (8.3.2018)
Quellen
Dieser Beitrag entstand nach einem Vortrag im Rahmen der Ringvorlesung „Forum Software und Automatisierung“ am IAS.
Vortragsdatum: 16.11.2017
Vortragender: Markus Rentschler, Balluf GmbH
Vortragstitel: Sensorvernetzung mit IO-Link und IO-Link wireless